Leading UK Radiopharmacy ready to go live with SPECTra LIMS
04/11/2021
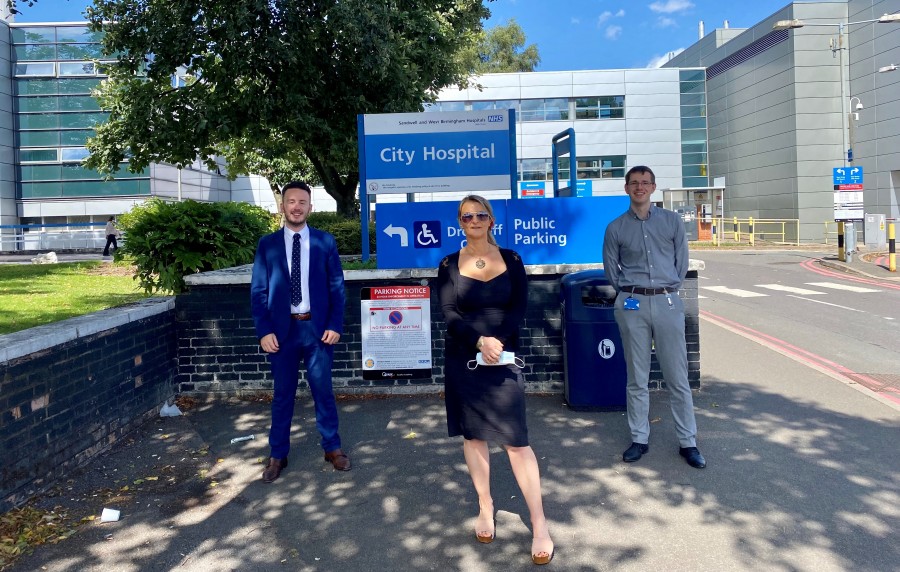
LabLogic is working closely with a number of leading radiopharmacies in the UK to develop the purpose-built LIMS software SPECTra. Leading the way is the Radiopharmacy at Sandwell & West Birmingham Hospitals NHS Trust who are nearing the end of their validation project.
The department is based at Birmingham City Hospital and is a central supplier to other hospitals in the local region, mainly manufacturing Tc-99m radiopharmaceuticals in multi-dose vials.
During a recent on-site IQ, SPECTra product specialist Adam Brown caught up with Head of Radiopharmacy Jilly Croasdale. Jilly is also the Lead Scientist for the Trust and Honorary Treasurer for the British Nuclear Medicine Society.
Here’s what she had to say:
Change in Radiopharmacy may be daunting but it's inevitable
“There is an appetite in UK radiopharmacy to move to more validated software and away from non-compliant practices like handwriting final product labels or using in-house software.
“Change can be quite daunting, but we have to embrace it. In the NHS we are constantly improving our care through new drugs and medicine, and we should be improving our systems in radiopharmacy.
Solving operational problems rather than creating them
“However, the big challenge is that we all work in our own unique way. I think SPECTra offers a good compromise between an entirely customised software package that is difficult to develop and hard to validate, to an off-the-shelf product that is too rigid and requires too many workarounds. I like that with LabLogic we are developing SPECTra to solve our operational problems rather than introducing new ones. This does not mean to say there won’t be challenges. Some ways of working may have to change, so it’s important to be flexible and keep an eye on overall service objectives rather than the minutiae of how things have historically been done.
Creating a quality product
“LabLogic has a track record with LIMS software, including one for PET applications which lots of sites around the world are using. However SPECT radiopharmacy is more complex in some ways, as it involves a greater number of products and radioactive raw material which is used for multiple production runs, for example so there are more variables. Although it has taken a while to get to where we are, I feel this is something that will work well and it’s worth the wait. I would much rather take the time to do it properly, and hopefully, this will mean that other sites in the UK will be able to implement the system much faster.
Moving from paper and an unvalidated system
"Like a lot of radiopharmacies in the UK, we are running software that is unsupported, unvalidated and high on the risk register. They work quite well for us for now, but it's unsustainable and not in line with the latest rules and regulations. When things go wrong it can cause real issues.
“This was our main driver for change, but we are using the opportunity to review our operation and look to improve quality.
Improved Business Intelligence
"One very important benefit of a system like SPECTra which was highlighted very recently when we had to collect a lot of data for the national radiopharmacy aseptics review conducted by NHSE. Because my current system does not allow data to be extracted easily or in a useful way, a lot of the information had to be estimated using paper records and a lot of counting! I look forward to being able to use our new SPECTra system to easily pull together activity data for my service. Going forward, business intelligence is going to become increasingly important and we need to be able to keep up with this in Radiopharmacy if we are going to take full advantage of any opportunities to develop our services.
Quality Improvements using SPECTra
“One of the benefits of SPECTra is that, while it required us to re-think workflows, it has meant we could look at the role our support worker carried out. Whereas before they were transcribing data onto final product labels, they can now be more focused on sanitation and transfers.
“Since we will be reducing manual transcription and duplication of data, the opportunity for errors will be reduced. For example, with the barcode driven inventory system, one scan of the barcode will bring the batch reference number, check the expiry date and decrement one from stock with 100% accuracy.
“Obviously having direct data capture from the dose calibrator and in-built automatic calculations in the software will reduce the risk of human error in radiopharmacy.
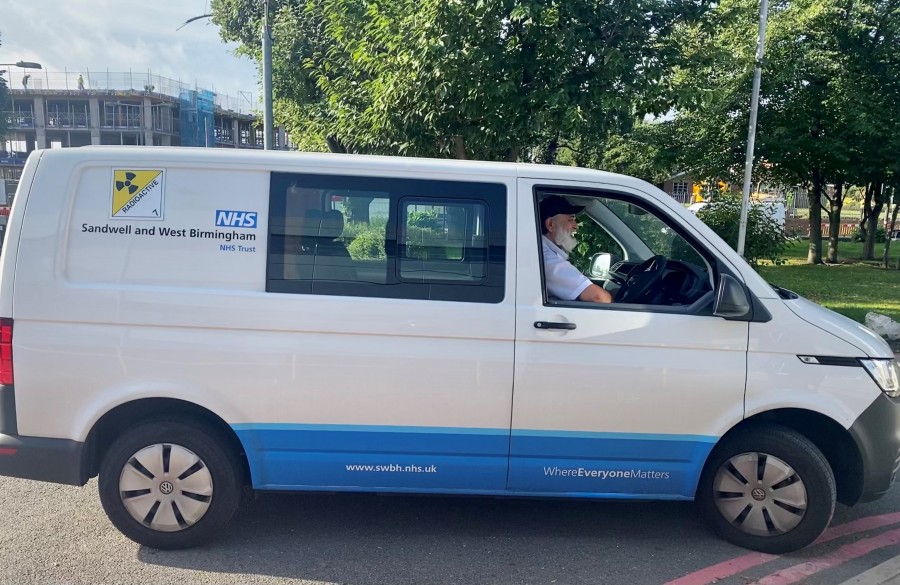
Hands-on training
“LabLogic recently delivered an on-site training session which I was very impressed with. They came prepared with training laptops that had SPECTra pre-loaded with our data. It gave everyone the chance to use the system and to see what we have been working on. I think it really helped people overcome any nervousness and I feel our team now are genuinely excited by what’s to come.
“As SPECTra is a purpose-built system, you really don’t have to be an expert in combining computers to use it. It was clear during the training that people found it pretty easy to pick up.
Face to face vs Online
“Throughout the process and the height of the Covid pandemic, we have done a lot of things online with LabLogic, which is great for convenience. However, you just can’t beat face to face contact for things like training, validation and getting a real understanding of what’s happening on-site. I think this is one of the benefits of having a UK based company for this project.
“I think LabLogic are a good company to work with, they have been patient with us, their staff are helpful and want to do a good job. I’m happy with where we are at with the system and am looking forward to getting things fully operational.”
SPECTra Product Specialist Adam Brown said, “Jilly and her team have been a pleasure to work with. They have embraced change and got to grips with how SPECTra works, which has allowed us to make some useful improvements. I’m looking forward to the team using it daily and making further improvements to their everyday life in the radiopharmacy.”
Look out for our next article, where we catch up with Operation Manager Shaun Johns who has played a leading role in configuring the workflow and validating the system at Birmingham City Hospital.